Game changing innovation in a Silicon Valley garage. Who would have thunk it?
From an energy efficiency perspective, one of the most persistently difficult appliances is the clothes dryer. Apart from switching from electricity to natural gas, or buying a washing machine that has extra high spin speeds, there just isn’t much you can do about dryer energy use. For decades people have talked about dryers that use a heat pump instead of electric resistance heating, but they suffer from long dry times, high cost, and reliability issues.
Now comes a new technology that promises to revolutionize drying efficiency: the long wave radiofrequency (RF) dryer. This technology involves using very long wave electromagnetic RF radiation (about 70 feet or 21 meters wavelength, corresponding to 13.56 MHz, for the technical folks in the audience) to heat the water in the clothes. One of the great advantages of such an approach is that the RF energy can be “tuned” to preferentially heat water, so it’s very efficient indeed.
On February 5th, 2014 I had occasion to visit a Silicon Valley garage containing an RF dryer prototype. The company is called Cool Dry RF, and they have made tremendous progress on this difficult problem.
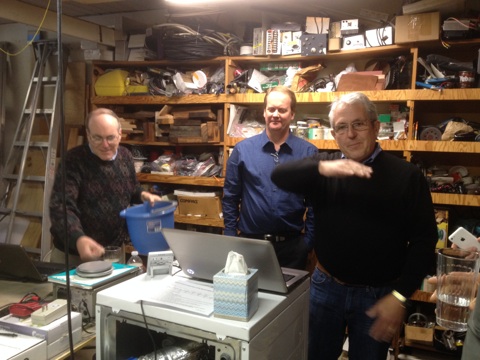
Photo credit: Jonathan Koomey.
Two of the three inventors of Cool Dry are in the picture: John Eisenberg (left) and Dave Wisherd (right). Chris Calwell of Ecova is in the center.
The first thing to understand is that the value of clothes moving through the clothes dryer is much higher than the value of the energy used to dry the clothes. Thus drying methods that are easier on the clothes (and extend clothing lifetime) have an inherent advantage.
RF dryers benefit from more direct coupling of drying energy to the water in the clothes, resulting in lower fabric temperature and fewer rotations. In addition, the technology allows the dryer to directly sense the capacitance of the load of clothing, giving a precise measurement of the actual moisture content of the clothes. By contrast, conventional moisture sensors (resistive strip sensors) are notoriously imprecise, and often result in over drying (and thus fabric damage).
These benefits together result in significantly improved drying performance. The RF Cool Dry prototype was built from a conventional 240 VAC GE Spacemaker electric dryer. The engineers bought and maintain a second dryer, which is the exact same model in a conventional configuration. The second dryer is the baseline against which savings are measured.
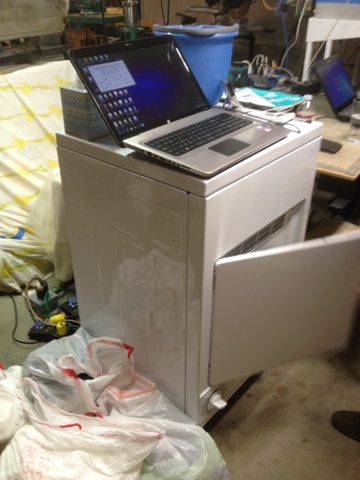
Photo credit: Jonathan Koomey.
The standard GE Spacemaker dryer, instrumented but otherwise unmodified.
When the Cool Dry prototype is compared to the conventional dryer for drying a 3 pound mixed load (denim jeans, cotton T-shirts, high speed washer spin), the results are striking. Drying time is the same (35 minutes), but electricity use is 26.5% lower for Cool Dry. In addition, 8.5 times fewer drum rotations and a 45 degree F lower fabric temperatures results in one fifteenth of the lint compared to the standard dryer. The more precise measurement and directed RF energy means that the T-shirts are not over-dried as they are in the conventional dryer.
Your clothes will therefore last longer with the RF dryer. This technology is yet another example where improved efficiency is a byproduct of good design, and in fact it’s the other benefits (longer clothing lifetimes) that will probably be most motivating for consumers (the lower cost of operation will be a bonus).
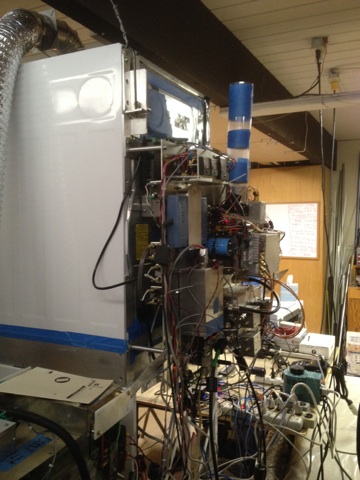
Photo credit: Jonathan Koomey.
The back of the modified GE Spacemaker dryer that incorporates the GE Cool Dry technology. Some of the wiring is for instrumentation, but most is to make the device function.
This system is by no means optimized. The Cool Dry engineers were forced by the limitations of the Spacesaver dryer to make certain compromises, and I’ll pretty sure that building the technology into a dryer design from the start will result in much bigger savings. The Cool Dry engineers didn’t want to say this definitively, because they are very careful fellows, but just take this as my speculation based on experience reviewing whole system design methods for improving efficiency. Starting from scratch almost always results in higher savings and lower costs.
The company is currently in licensing discussions with several big appliance companies, so there’s a good chance this innovation will make it to market. There is a long road between a prototype and commercialization, but this looks like an innovation that has legs. That’s hopeful, given how hard it’s been to improve dryer efficiency in the past. Let’s hear it for garage-based innovation, whole system design, and thinking outside the box!
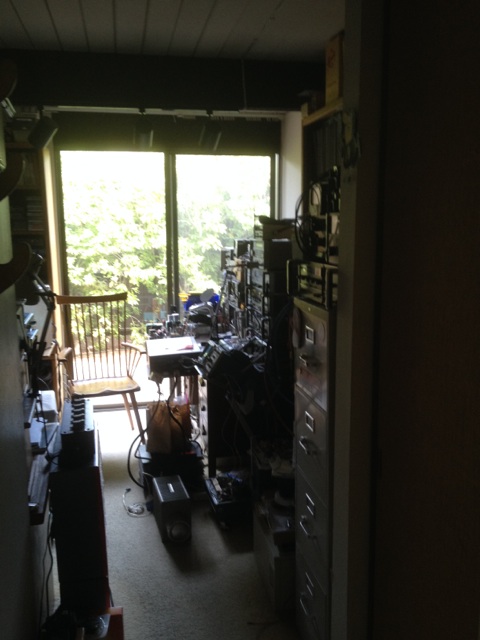
Photo credit: Jonathan Koomey.
Now that is my kind of workshop!
Addendum: The earlier version of this post gave the wavelength of the RF waves as 70 meters, but the correct wavelength is 70 feet, as now described above.